Plastics and Polymers - What's the Difference?
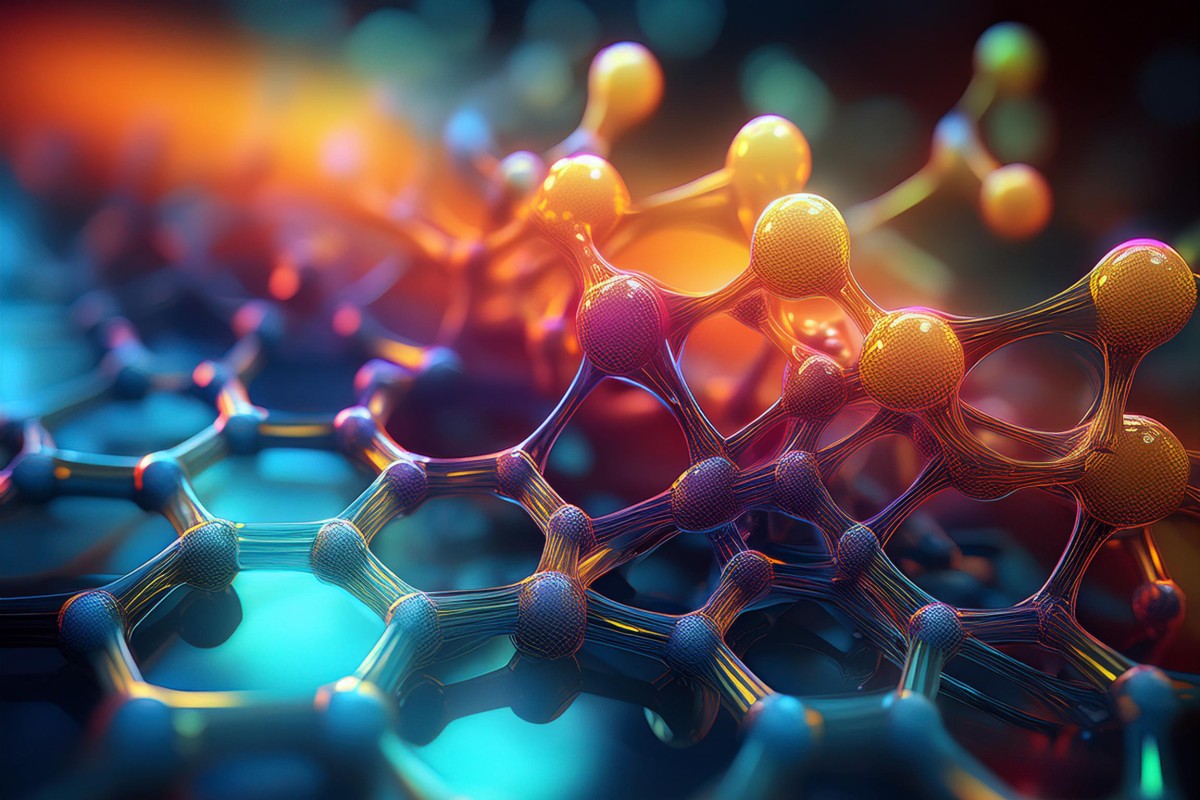
Understanding the difference between plastics and polymers requires a foundational knowledge of what polymers are and how they relate to plastics.
Polymers are large molecules composed of repeating structural units called monomers, connected by covalent chemical bonds. These macromolecules can be either natural, like DNA, proteins, and cellulose, or synthetic, such as plastics and nylon. The diverse nature of polymers allows them to exhibit a wide range of physical properties, making them indispensable in various industries, including healthcare, automotive, construction, textiles, and many more.
Polymers are categorised based on their origin (natural or synthetic), structure (linear, branched, or cross-linked), and behaviour under heat (thermoplastic or thermoset). Natural polymers include rubber and silk, while synthetic polymers encompass a wide range of materials including plastics, synthetic fibers, and elastomers.
Plastics, which are a specific category of synthetic polymers, are known for their versatility, durability, and moldability. Created through the polymerisation or polycondensation of organic raw materials such as cellulose, coal, natural gas, salt, and crude oil, plastics are ubiquitous in modern life. The term “plastic” originates from the Greek word “plastikos,” meaning capable of being shaped or molded, highlighting their key characteristic.
The most common types of plastics include polyethylene (PE), polypropylene (PP), polyvinyl chloride (PVC), and polystyrene (PS). Polyethylene, the most prevalent plastic, is used in products including plastic bags, bottles, and toys due to its flexibility and moisture resistance. Polypropylene, known for its toughness and chemical resistance, finds applications in packaging, textiles, automotive parts, and reusable containers. Polyvinyl chloride is a hard plastic used in construction materials, including pipes and fittings, and is valued for its durability and resistance to environmental degradation. Polystyrene is utilised in products such as disposable coffee cups, plastic food boxes, and insulation materials for its rigidity and thermal insulation properties.
Polyethylene terephthalate (PET), acrylic, and nylon are also notable plastics. PET is widely used in beverage bottles, food containers, and synthetic fibres for its strength, thermo-stability, and transparency. Acrylic plastics are known for their clarity and resistance to impact and weathering, while nylon is a strong, flexible plastic used in textiles, automotive parts, and mechanical components like gears and bearings.
A common question is, “Is plastic a polymer?” The answer is yes. However, it is important to note that not all polymers are plastics. Plastics are a subset of polymers distinguished by their ability to be moulded or shaped under heat and pressure. This property, combined with their lightweight, strength, and resistance to chemicals, makes plastics suitable for a wide array of applications, from everyday household items to specialised industrial components.
So what is a Polymer Masterbatch?
A polymer masterbatch is a concentrated mixture of pigments, additives, and polymers that is used to impart colour and enhance the properties of plastic materials during manufacturing. This masterbatch is created by blending pigments or additives with a carrier resin through a heat process, resulting in a uniform, concentrated granule. These granules are then mixed with raw plastic resin in a precise ratio to achieve the desired colour and functional properties in the final product. Masterbatches offer several advantages, including consistency in colour and performance, ease of use, and reduced processing costs. By incorporating masterbatches, manufacturers can efficiently produce high-quality, customised plastic products with enhanced characteristics, such as UV resistance, flame retardancy, or improved mechanical strength.
Antimicrobial Masterbatch
Antimicrobial masterbatch is a specialised type of polymer masterbatch designed to impart antimicrobial properties to plastic products. It contains additives, such as Biomaster, that inhibit the growth of bacteria, fungi, and other microorganisms on the surface of the plastic. When integrated into plastic resins during manufacturing, antimicrobial masterbatch provides long-lasting protection against microbial contamination, reducing the risk of unpleasant odours, discolouration, and degradation of the material. This makes it particularly valuable for applications in healthcare, food packaging, and high-touch surfaces where hygiene and safety are critical. By incorporating antimicrobial masterbatch, manufacturers can enhance the durability and cleanliness of their products, ensuring they meet stringent health and safety standards while extending their functional lifespan.
Find out more about our Biomaster Antimicrobial Technology HERE
Glossary
Plastic: A synthetic material made from a wide range of organic polymers, such as polyethylene, PVC, nylon, etc., that can be moulded into shape while soft and then set into a rigid or slightly elastic form.
Polymer: A large molecule composed of repeating structural units (monomers) connected by covalent chemical bonds. Polymers can be natural, like DNA and cellulose, or synthetic, like plastics and nylon.
Monomers: Small molecules that can join together to form polymers. Monomers act as the building blocks of polymers.
Macromolecules: Extremely large molecules composed of thousands or even millions of atoms. Polymers are a type of macromolecule.
Polymerisation: A chemical process that combines small molecules (monomers) into a covalently bonded chain or network, forming a polymer.
Polycondensation: A type of polymerisation process where monomers join together with the simultaneous elimination of small molecules such as water, alcohol, or hydrogen chloride.
Thermo-stability: The ability of a substance to retain its physical and chemical properties at elevated temperatures. In the context of polymers, it refers to the resistance to decomposition or chemical change under heat.
Masterbatch: A concentrated mixture of pigments and additives encapsulated during a heat process into a carrier resin, which is then cooled and cut into granules. Masterbatches are used to colour or enhance the properties of plastics during the manufacturing process.
Additives: Substances added to polymers to modify their properties. Common additives include stabilisers, plasticisers, flame retardants, and UV absorbers, which enhance the performance and durability of plastic materials.
Elastomers: A category of polymers that exhibit elastic properties, meaning they can return to their original shape after being stretched or deformed. Common elastomers include natural rubber and synthetic rubber.
Resins: Organic compounds that can be transformed into plastics through polymerisation. Resins are used as the base material in the production of plastics, and they can be either thermoplastic or thermosetting.
Smart Polymers: Polymers that respond to environmental stimuli, such as changes in temperature, pH, or light. These materials can change their properties in response to external conditions, making them useful in applications like drug delivery and environmental sensing.
Recycling: The process of collecting, processing, and reusing plastic materials to create new products. Recycling helps reduce the consumption of raw materials, decrease energy use, and minimise plastic waste in landfills and oceans.
Circular Economy: An economic system aimed at minimising waste and making the most of available resources. In the context of plastics, a circular economy focuses on designing products for durability, repairability, and recyclability, as well as promoting the reuse of materials.
Elastomeric Polymers: Polymers characterised by their elastic properties, allowing them to stretch and return to their original shape. These are commonly used in products like gaskets, seals, and flexible tubing.
Cross-Linking: A chemical process where polymer chains are interconnected through covalent bonds, forming a three-dimensional network. Cross-linked polymers, or thermosets, have enhanced strength and stability but cannot be re-melted or re-molded.
Thermoplastics: Polymers that become soft and moldable upon heating and solidify upon cooling. They can be re-melted and re-shaped multiple times, making them versatile for various applications. Examples include polyethylene and polyvinyl chloride.
Thermosets: Polymers that, once set into a shape through heat and chemical reactions, cannot be re-melted or re-molded. They are known for their rigidity and durability, with common examples including epoxy and phenolic resins.
Blends: Combinations of two or more different polymers to achieve desirable properties that are not possible with a single polymer alone. Polymer blends can be tailored to meet specific performance requirements.
Composite Materials: Materials made from two or more different substances, where each contributes distinct properties. For example, fiberglass composites combine glass fibres with a polymer matrix to enhance strength and durability.
Further Reading
1. Plastics and Polymers: What is the Difference? Material Innovation Insights. https://www.material-innovation-insights.com/articles/plastics-and-polymers-what-is-the-difference
2. Introduction to Polymers by Robert J. Young and Peter A. Lovell. Available on Google Books
3. Journal of Polymer Science Articles. Available on Wiley Online Library
4. ScienceDirect Articles on Polymers. Available on ScienceDirect
What Next?
🔗 Follow us on Social Media, here is our LINK TREE
✉️ See how our additive technology can benefit your business by CONTACTING US
🦠 Find out more about Biomaster Antimicrobial Technology HERE
🎥 Watch our video on how Biomaster works WATCH NOW
📰 Subscribe to our Newsletter - SUBSCRIBE
← Back to blog